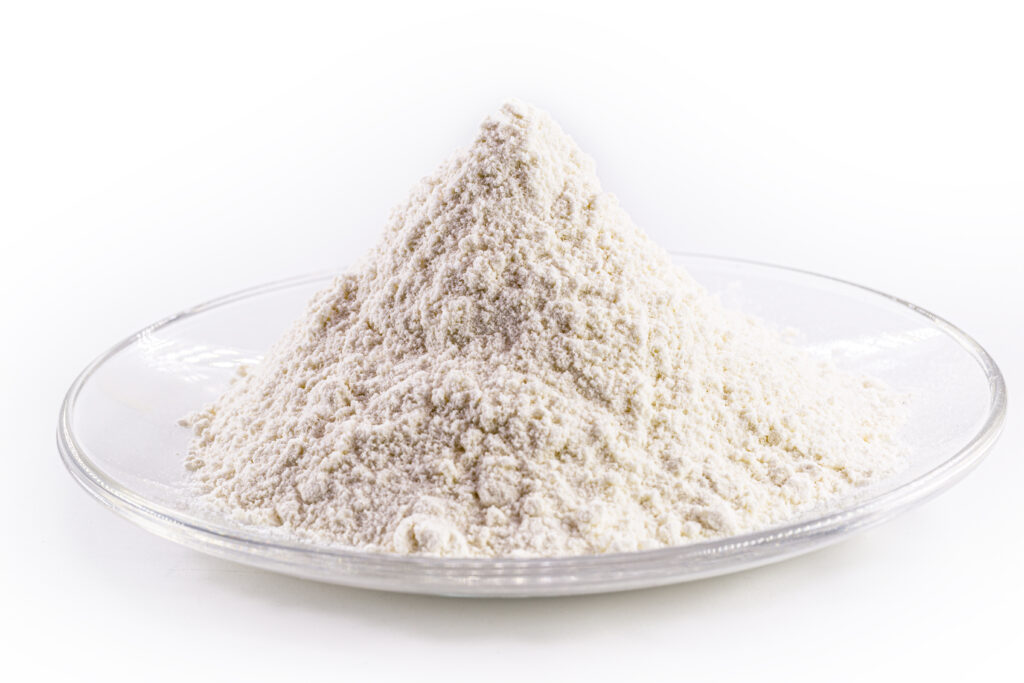
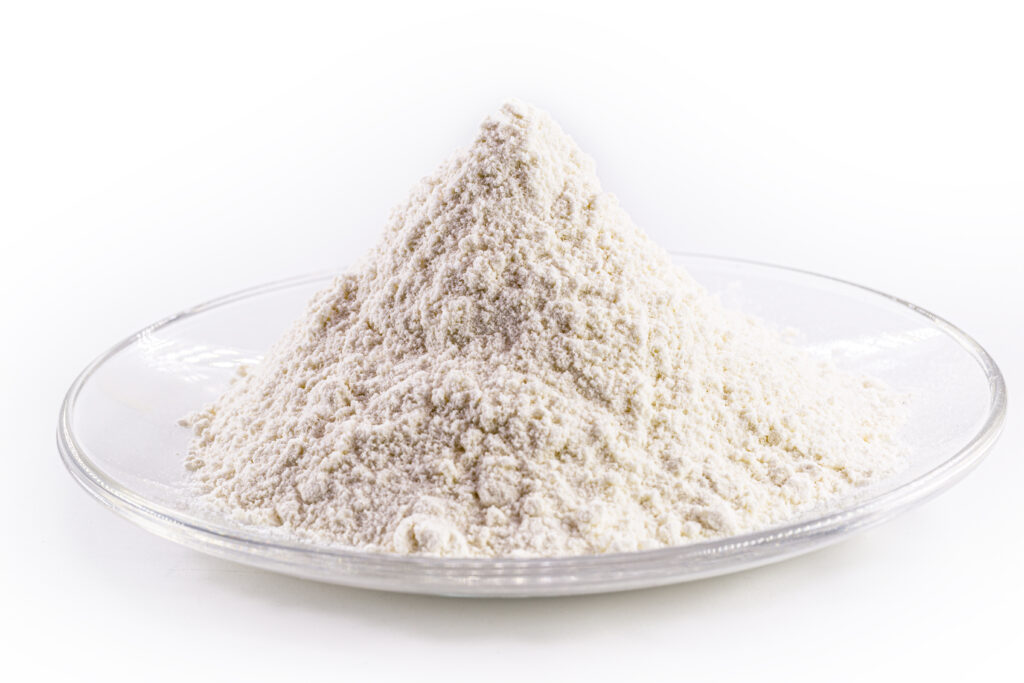
Soda ash, also known as sodium carbonate, is an inorganic compound that is widely used across the globe. It has a long history of use, dating back to ancient civilizations where it was used to make glasses and clothes. Initially, soda ash was produced from the ash of a plant that grew in sodium-rich soils. However, with the advent of the Industrial Revolution, the method of production changed to a more industrial manufacturing process.
There are several methods used to produce soda ash today, including the extraction from trona, the LeBlanc process, the Solvay process, and the Hou process. The extraction of soda ash from trona, also known as natural soda ash production, is commonly used in the United States and Turkey. Trona can be found in lake brines or mineral deposits, and the largest deposits are located in Wyoming, USA and Ankara, Turkey. Trona extraction accounts for more than 30% of global soda ash production.
The process of natural soda ash production involves injecting heated water into the trona deposits to create a brine solution. From there, the brine undergoes filtration, crystallization, separation, and drying to form the soda ash. Another method, the Solvay process, also known as the ammonia-soda process or synthetic soda ash process, uses brine, limestone, and ammonia as the main raw materials. It accounts for more than 70% of soda ash production worldwide and consists of four main processes: ammoniation, carbonation, and calcination.
In 1930, Chinese scientist Hou Debang developed a new method for producing soda ash known as the Hou process. This process uses carbon monoxide to produce carbon dioxide instead of limestone, resulting in the elimination of calcium chloride as a byproduct. Ammonia chloride becomes the byproduct of this process instead. Despite its success, scientists and engineers continue to work on developing new methods that increase the efficiency of soda ash production while also considering environmental safety
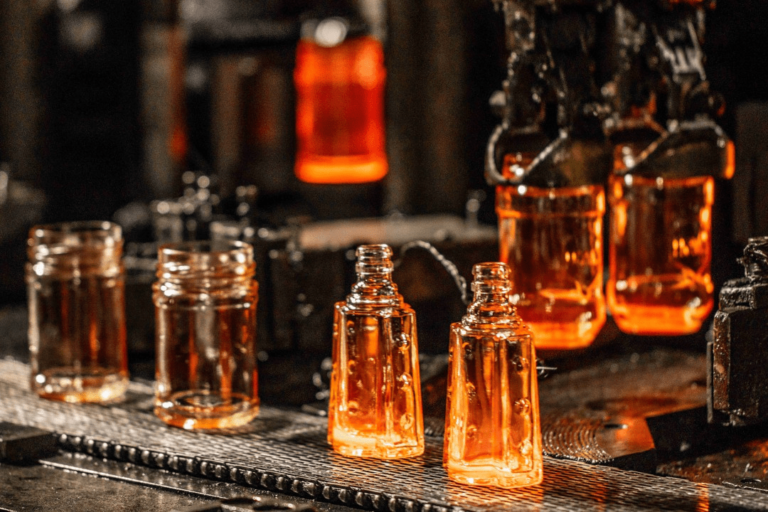
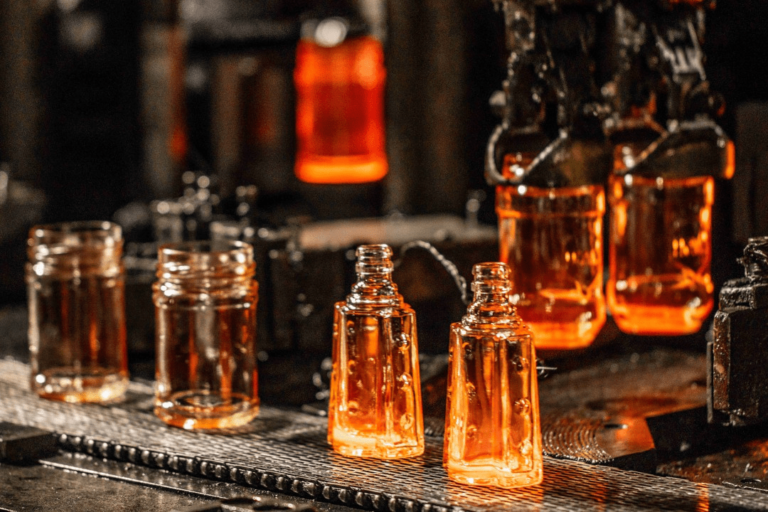
The glass manufacturing industry is experiencing a period of significant growth, fueled in part by a rise in industrial production and favorable policies and initiatives implemented by governments around the world. In 2022, the glass manufacturing market is valued at US$265.6 billion and is expected to surpass US$460 billion by 2032. This growth is being driven by a number of factors, including an increase in demand for flat glass in the construction sector.
Flat glass, which is used in a variety of applications including building, furniture, construction, and automotive, is typically manufactured using the float process, which accounts for nearly 95% of all flat glass production. Float glass is known for its high luminescence and ability to be produced in a range of colors, as well as its flexibility in terms of light refraction and opacity. These characteristics make it an ideal choice for use in architecture and construction.
The automotive and transportation sector is also expected to be a major contributor to the growth of the glass manufacturing industry, with the sector’s share of the market predicted to rise above 5.5% between 2023 and 2032. Glass is extensively used in the construction of vehicle windows and windshields, and with car sales on the rise in Latin America and ASEAN countries, demand for auto glass is expected to be strong.
In addition to its use in the automotive sector, glass is also in high demand in the aerospace industry for use in the construction of aircraft cabin interiors, engine components, liners, and exhaust system components. The European glass manufacturing market, which is already one of the largest in the world, is expected to exceed US$115 billion by 2032 and is expected to see a boost in demand from the automotive and aerospace sectors. In 2021, the European container glass business saw the highest production growth rate, producing more than 23.4 million tons of bottles and jars to meet domestic and international demand.
To facilitate the expansion of the glass manufacturing industry and increase production capacity, many companies are implementing strategic expansion initiatives to gain a competitive advantage. As the demand for glass continues to grow, the industry is expected to remain dynamic and energetic in the years ahead.